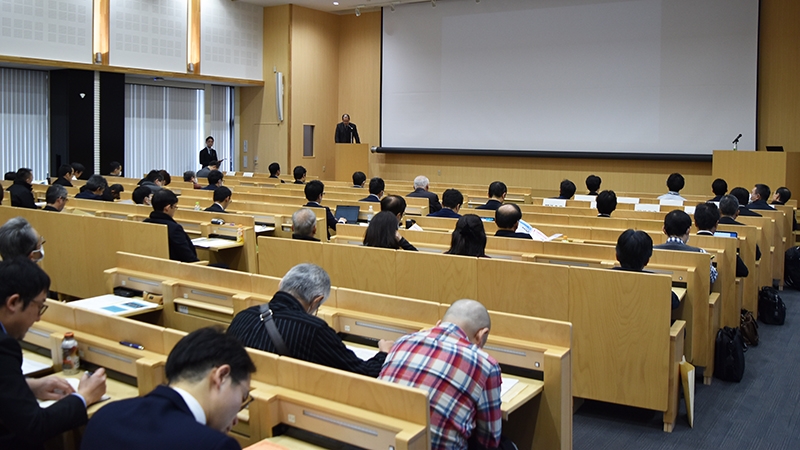
どうやってロボット入れた? 導入事例セミナーに関心集まる/名古屋市
名古屋市は2月10日、同市昭和区の名古屋工業大学で「ロボット・IoT・サイバーセキュリティ導入事例セミナー」を開催した。同大学が運営する「ロボット・IoT・サイバーセキュリティ専門人材育成講座」を受講した企業の担当者が講師を務め、自社のロボット導入事例やモノのインターネット(IoT)システムの導入事例を報告し、参加者の関心を集めた。
生産現場のロボット化と自動化を支援するウェブマガジン
RECENT POSTS
名古屋市は2月10日、同市昭和区の名古屋工業大学で「ロボット・IoT・サイバーセキュリティ導入事例セミナー」を開催した。同大学が運営する「ロボット・IoT・サイバーセキュリティ専門人材育成講座」を受講した企業の担当者が講師を務め、自社のロボット導入事例やモノのインターネット(IoT)システムの導入事例を報告し、参加者の関心を集めた。
ロボットのシステムインテグレーター(SIer、エスアイアー)の業界団体であるFA・ロボットシステムインテグレータ協会(SIer協会、会長・久保田和雄三明機工社長)は1月30日、名古屋市中区で「SIer’s Day(エスアイアーズデー)in なごや だがね」を開催した。153人が参加し、会場は盛り上がった。
産業用ロボットを導入した現場をリポートする連載「ロボットが活躍する現場」も11回目を迎えた。今回は石川県かほく市に本社を構える梶製作所(梶政隆社長)を訪ねた。同社は繊維機械を中心とした各種産業用機械の製造と、金属部品の加工を事業の2本柱に掲げる。梶司郎専務は、加工事業の工場を「将来は省人化や省力化のモデル工場にしたい。子供たちにも興味を持ってもらえるような『ワクワクする工場』を目指す」と意気込む。その将来構想への種まきの一環で、ロボットを使った自動化システムを2018年12月に導入した。
マリノプロジェクト(神戸市西区、亀田真嗣社長)は、産業用ロボットでウレタンや発泡スチロール、人工木材のケミカルウッドなどを切削加工し、自動車の車体パーツ、ロケットの模型、機械の試作部品などさまざまなものを製作する。ドイツのロボットメーカー、KUKA(クカ)の可搬質量125kgのロボットに加工ユニットを装着し、1辺が1mを優に超えるワーク(被加工物)も加工できる。「大型ワークを一体で形状加工できる点でこのロボット切削システムは貴重な存在であり、家具や模型メーカーなど新しい顧客、顧客層の開拓にも役立っている」と亀田社長は話す。
日産自動車の横浜工場は、2014年から協働ロボットを使った自動化に取り組む。製造部に新設された「革新製造技術チーム(革新チーム)」が中心となり、これまでに4つの協働ロボットシステムを構築した。前編で解説した第1弾と第2弾に続き、後編では第3弾と第4弾を紹介する。「台車に載せて移動式にしたり、人が近くにいても作業を継続するなど、常に新たなことに挑戦している」と革新チームリーダーの白石京専門工長は言う。
日産自動車の横浜工場は、2014年から協働ロボットを使った自動化に取り組む。製造部に新設された「革新製造技術チーム(革新チーム)」が中心となり、これまでに4つの協働ロボットシステムを構築した。エンジンの組み立て工程の一部を協働ロボットが担う。「狭い空間で人と一緒に働ける協働ロボットは、既存の生産ラインを変えずに製造工程の改善ができる」と革新チームリーダーの白石京専門工長は言う。
産業用ロボットを導入した現場をリポートする連載「ロボットが活躍する現場」。今回は埼玉県入間市にあるテラダイ(寺園智樹社長)を訪ねた。ダイカストと呼ばれる金属の成形加工が得意な同社。2017年、検査工程までを含めた無人化を目指し、自動車部品の生産ラインで新たなロボットシステムを導入した。今のところ、全てが計画通りとはいかないが、「自動車産業の変化に備えて、汎用性の高いシステムを導入した」と将来を見据える。
アマダ土岐事業所の金型工場「T876工場」がフル稼働を続ける。24時間、365日の稼働で、タレットパンチプレス用金型の生産能力を従来の1.5倍にあたる月産3万本、一人当たりの生産高4倍を実現した。しかも常時工場にいる人員はたった3人で、顧客からの注文を受けて最短3時間で出荷できる。最新鋭の自動化工場を取材した。
安川電機は2018年7月、埼玉県の入間事業所内に「安川ソリューションファクトリ」を完成させた。デジタルデータの活用でより生産性を高める「「i³-Mechatronics(アイキューブメカトロニクス)」の考え方を具現化した工場だ。「モノのインターネット(IoT)やビッグデータ、人工知能(AI)などの技術を使い、生産性は3倍、リードタイムは6分の1を実現した」と白石聡工場長は言う。
岡本工機(広島県福山市、菊地正人社長)は、歯車や受注生産の工作機械を製造するメーカーだ。広島県内に3つの工場を構え、本社工場や尾道工場ではそれぞれ10台ほどの産業用ロボットが稼働し、府中工場にも協働ロボットシステムなどを導入した。「ロボットがあると生産量も品質も安定する。システム構築や動作変更を自分たちでこなせることが重要」と菊地社長は話す。